PILE FOUNDATION
Pile foundations are type of deep foundation which are used to support heavy structures and buildings in areas with weak soil or unstable ground conditions.
Types of Pile
- Sheet Piles
- Load Bearing Piles
- End bearing Piles
- Friction Piles
- Soil Compactor Piles

Machinery Required
- Pile drilling machine
- Poclain
- JCB
- Dumpers
Procedure For Construction of Cast In Situ Pile
1. Setting Out
- Prior to commencement of the piling work the main contractor shall setout the main grid line, provide an agreed datum level and afford facilities for the piling contractor
- A survey point is provided at centre of pile with atleast 2 reference points to maintain its original position

2. RIG Movement Sequence
- Based on the important of the individual structure, the critical pile to be cast first shall be identified.
- Drilling with pile Auger is carried out into Clay/sand and goes upto Hard Rock.
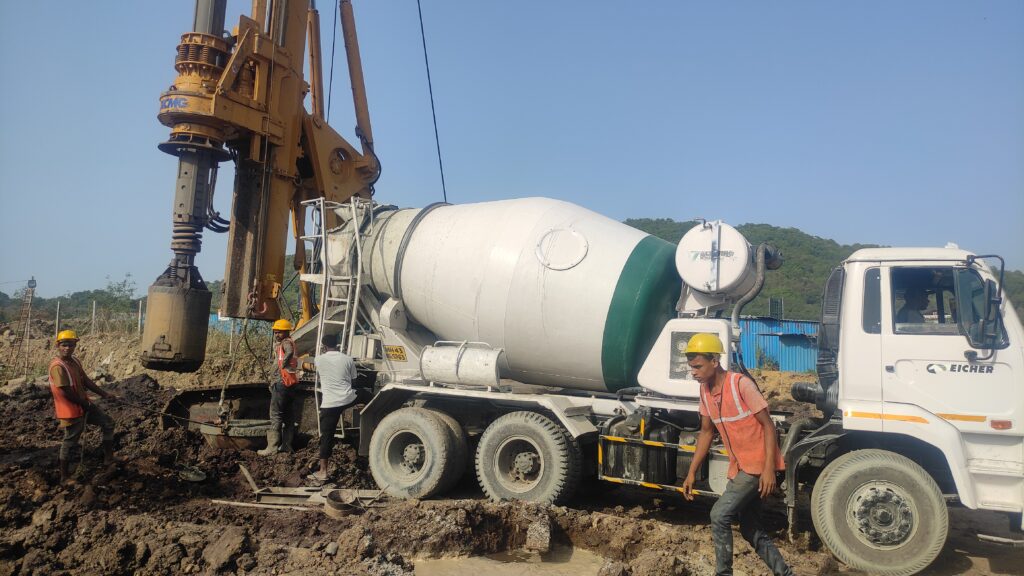
3. BENTONITE Preparation ( If applicable )
- Bentonite tank shall be established at site before commencement of piling activities.
- Bentonite head should be 1.5m above ground water level.
- The bentonite will be mixed, in the predetermined ratio, with water in the high turbulence colloidal mixer thus ensuring the complete dispersion of the bentonite particles

4. Pile Point Fixing
- At each location pile point to be marked as per drawing
5. Boring Using Hydraulic Rig
- The RIG to initiate the boring of the pile at center point fixed
- Temporary or permanent Liner is fixed upto point of Refusal(Hard strata) to avoid any soil collapse and maintain verticality of pile.
- Auger Drilling is continued in hard rock upto Required Socket length as per Design.
- Muck is removed from inside the Liner with help of bucket
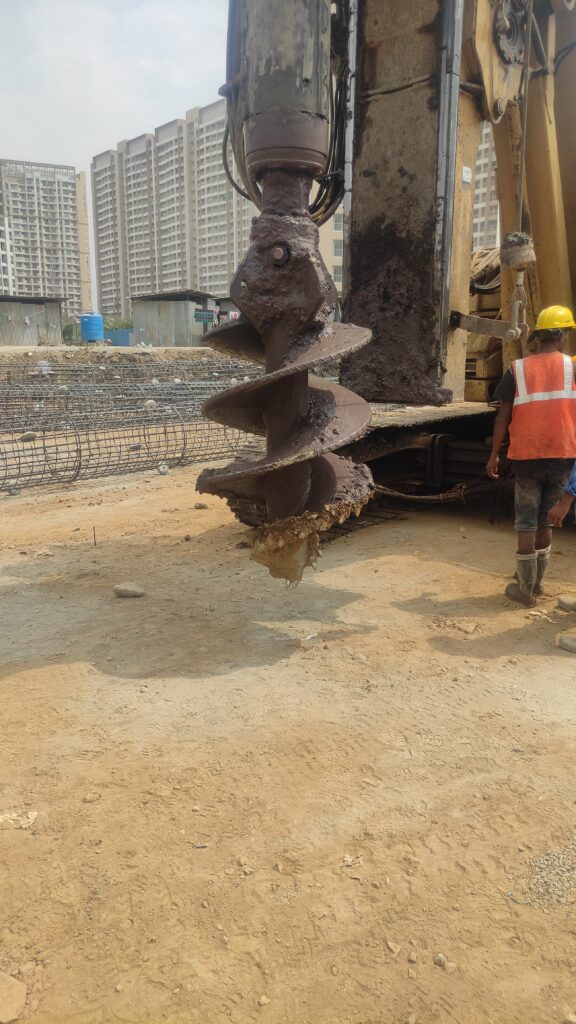
6. Boring Using Direct Mud Circulation (DMC)
- Excavate the soil from the inner of the already placed casing up to 2 to 3 m depth below the casing bottom.
- Cut a square hole of 150 mm width in the casing from the working platform top level to allow bentonite overflow to get out from the pile borehole.
- After guide casing driving, the bailer is taken out from the borehole, and boring is continued by percussion hammering with the help of a chisel by pumping Bentonite slurry having a specific gravity of 1.03 to 1.08 through the DMC rods connected.
- Simultaneously, the bentonite slurry that dislodged from the borehole flows out from the casing hole into the settling tank through the trenches made before operation.
- This process is continued until the boring is completed.
- Then the DMC pipes and chisel are removed. After completion of boring, bore depth should be measured by the sounding chain.

7. Pile Termination
Pile can be terminated earlier with minimum 1D socket in hard rock if pile penetration is less than 20CM in 10Mins of drilling for 3 consecutive times
8. Cage Lowering
Reinforcement cage as per design is shifted with help of JCB and inserted inside Liner upto refusal
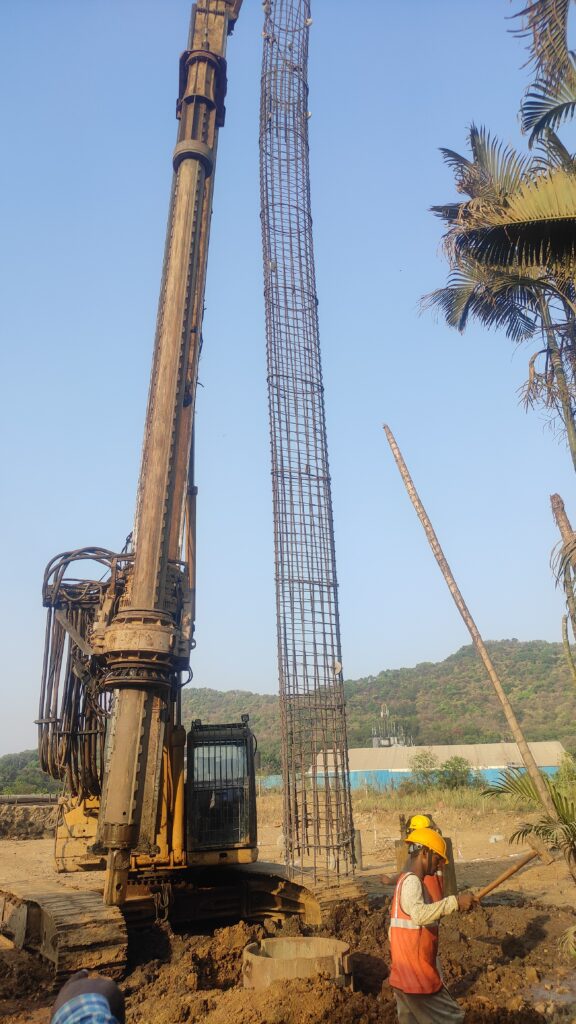
9. Flushing of Bore Stabilized by Bentonite
- As piles are in sandy/silty strata (friction piles), it is always necessary to carry out flushing of piles at the end of completion of the pile borehole with fresh bentonite through the DMC rod connected.
- For flushing, bentonite slurry will be directly pumped from the swelling tank, where the slurry is ready for use after swelling.
- Air flushing will attract side collapses, hence not to be used for flushing and even flushing with immature fresh bentonite slurry.
- After cage lowering, tremie pipe lowering will be completed.
- Flushing will be done through already placed tremie before concreting.
- The bentonite coming out from the borehole will join the regular “vertical pump tank”. Frequently checking the specific gravity of bentonite slurry being fed v/s coming out of the borehole is necessary. When both the specific gravities match, the flushing is declared over.
- Return bentonite slurry, which is contaminated and contains much silt stored in a vertical pump tank, can be reused by recycling with the help of a vertical pump and desander unit.
10. Pile Concreting
- For concreting Treimie method is used in which Treimie is strictly kept short by 300mm
- Pile casting is done by Concrete slump maintained between 150mm-200mm.
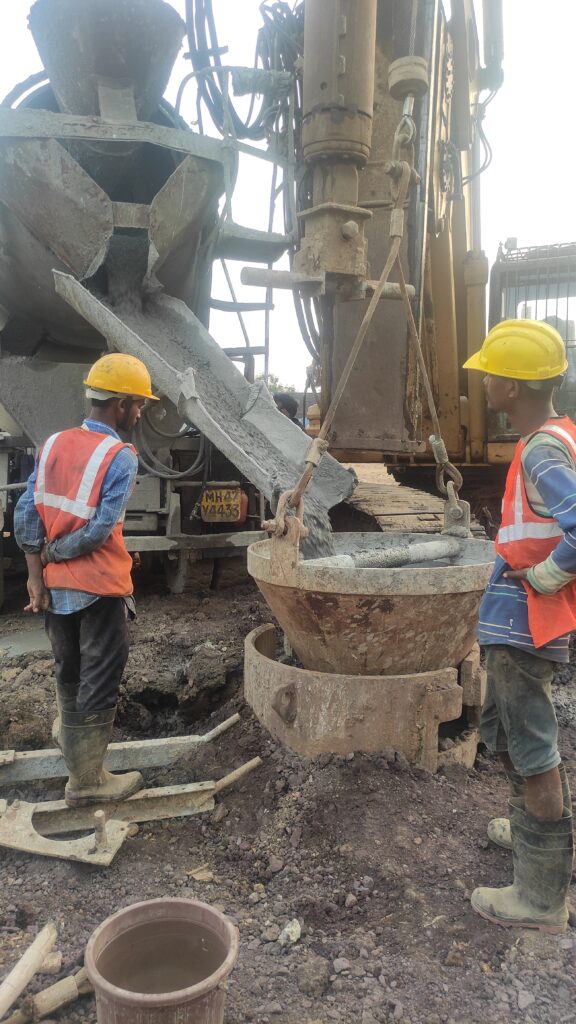
11. Chipping of Pile Head
After casting Pile is break upto cut-off level which then forms development length for Raft foundation above
12. Pile Growing
Pile growing shall be done if hard and good quality concrete not achieved at cut off level after pile top chipping
13. Muck Removal
The Contaminated bentonite slurry is not ecofriendly and hence this slurry has to be disposed safely